We have developed a metal membrane that could accelerate the roll-out hydrogen fuel cell vehicles, and potentially develop a new export market for Australia.
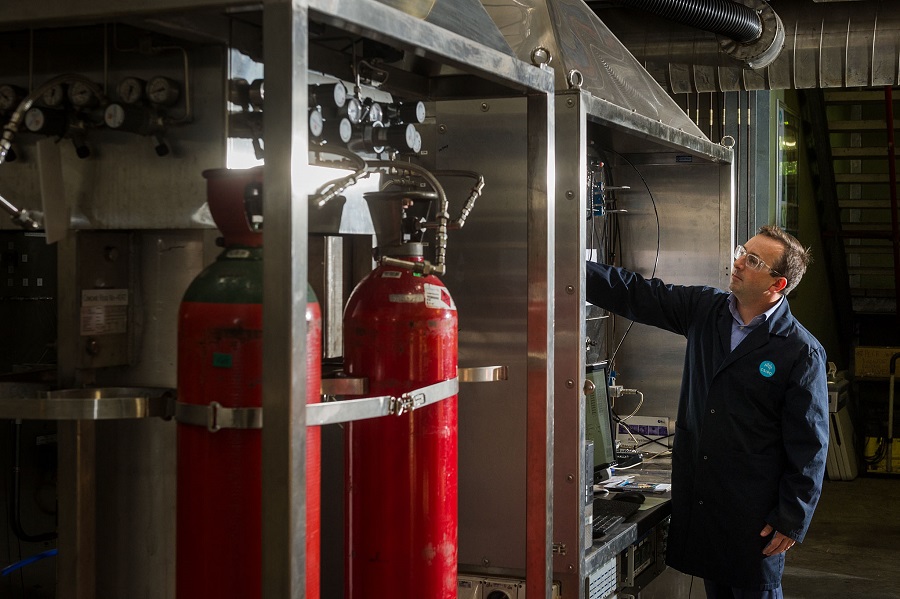
Photo of CSIRO researcher in hydrogen lab.
Dr Michael Dolan in our hydrogen lab.
It’s colourless, odourless, the most abundant element in the universe, and may one day take you from 0-100 on the highway. It seems as though hydrogen is a pretty logical choice for clean fuel of the future. The kicker is that there’s very little pure hydrogen to be found anywhere on Earth, meaning we need to somehow produce it.
There are a couple of different ways to produce pure hydrogen – it can be extracted from natural gas, though carbon dioxide is a by-product. There’s also a renewable option through the electrolysis of water, which produces hydrogen and oxygen. Forcing this reaction requires a fair amount of energy which could potentially come from a clean source, like solar.
Then there’s the matter of transporting that pure hydrogen to the places it’s needed, and if we’re planning a hydrogen-powered vehicle revolution, that means every service station! Because of its low density, hydrogen can be difficult to transport and must be pressurised, and then carried by pipeline, tanker or some other secure method. While hydrogen is already being used around the world, the existing transport infrastructure is not enough to support widespread consumer use. As a standalone hydrogen delivery system, this isn’t shaping up to be cost or energy efficient.
But rest assured there are other options … ammonia for example. Ammonia is a compound of nitrogen and hydrogen that is already transported far and wide for use in industry (as fertiliser, cleaner, etc). What if we could piggyback this existing infrastructure and transport the hydrogen within the ammonia, and then extract the hydrogen from the ammonia at, or near, the point we need it?
We have spent many years researching the best ways to separate pure hydrogen from mixed gas streams, but in this case we’re separating high-purity hydrogen from ammonia. For this very purpose, we’ve developed a thin metal membrane that allows hydrogen to pass, while blocking all other gases.

An animation shows ammonia molecules passing through a membrane to become hydrogen.
Decomposed ammonia passes through our membrane, becoming pure hydrogen.
Our membrane means that hydrogen can be transported in the form of ammonia (which is already being traded globally), and then reconverted back to hydrogen at the point of use.
While Australia is a relatively small hydrogen market, the fuel can be distributed to emerging markets in Japan, South Korea and Europe using existing infrastructure. Thinking big, we could transport Australian-made ammonia around the world so that international fuel cell vehicles could run on our hydrogen. And if we’re creating the hydrogen renewably with solar power, we are essentially exporting Australian sunshine! How’s that for home-grown ingenuity?
Our Chief Executive Dr Larry Marshall is excited by the prospect of a growing global market for clean hydrogen, and the potential for a national renewable hydrogen export industry.
“This is a watershed moment for energy, and we look forward to applying CSIRO innovation to enable this exciting renewably-sourced fuel and energy storage medium a smoother path to market,” said Dr Marshall.
Our membrane has been welcomed by industry and is supported by BOC Gas, Hyundai, Toyota and Renewable Hydrogen Pty Ltd. The project also recently received $1.7 million from the Science and Industry Endowment Fund (SIEF), which will be matched by us.
In addition to our new membrane, we’re looking forward to applying our expertise to all stages of the hydrogen technology chain (including solar photovoltaics, solar thermal, grid management, water electrolysis, ammonia synthesis, direct ammonia utilisation via combustion and/or fuel cells, as well as hydrogen production).
13th March 2019 at 5:05 pm
Thank God you people are onto it. We are running out of time. Stationary use for EV charging sounds like the go. I think you need to get a demonstration charging station up and running with the membrane converting Ammonia asap. Once people see it in action they will get on board. This in effect could be a packaged fuel stop dropped off and installed anywhere in Australia where a truck can deliver ammonia-correct?
Pingback: Hydrogen Fuel from Ammonia |
16th November 2018 at 7:45 am
Maybe you could use a combination of heat (solar), salt, catalyst (cobalt/phosphorus), and radio (microwave) vibration
to shake apart water for reducing electicity. Anything along these lines?.
27th September 2018 at 2:22 pm
Ammonia ammonia could also be the foremost misunderstood compound that happens naturally in a very functioning marine museum. it’screated by most of the inhabitants in any body of water, and is very essential to know for the start aquarist and his initial tank. Ammonia may be a highly regarded compound to check in a very new marine museum, however what ought to be done with those results isn’t invariably as clear for the novice aquarist.http://www.mysoreammonia.com/
25th September 2018 at 8:58 pm
It is interesting that CSIRO is talking about a stationary application of ammonia to high purity hydrogen, for a fuel station. When it seems it would be possible to put the NH3 – H3 converter directly in front of the fuel cell that could go in the vehicle.
Why worry about having a high purity storage tank on board a vehicle when you could just convert ammonia as required ?
28th September 2018 at 4:09 pm
Hi Daniel, thanks for the comment. We passed it on to our researchers who provided this response:
“This would be a very elegant solution but there are some barriers to overcome before it would be possible. Making a mobile fuel conversion device adds more complexity as it requires the ability to rapidly heat up to operating temperature, then cool down again, many times a day. It also requires that the device is resistant to the vibrations and shock that vehicles experience. These factors create a lot of stress on the materials, and we’re still working on making the technology more robust so that it could be used onboard a vehicle. This approach may work for ships and trains which operate more continuously than the family car.”
Thanks, CSIRO social media team.