We have developed a metal membrane that could accelerate the roll-out hydrogen fuel cell vehicles, and potentially develop a new export market for Australia.
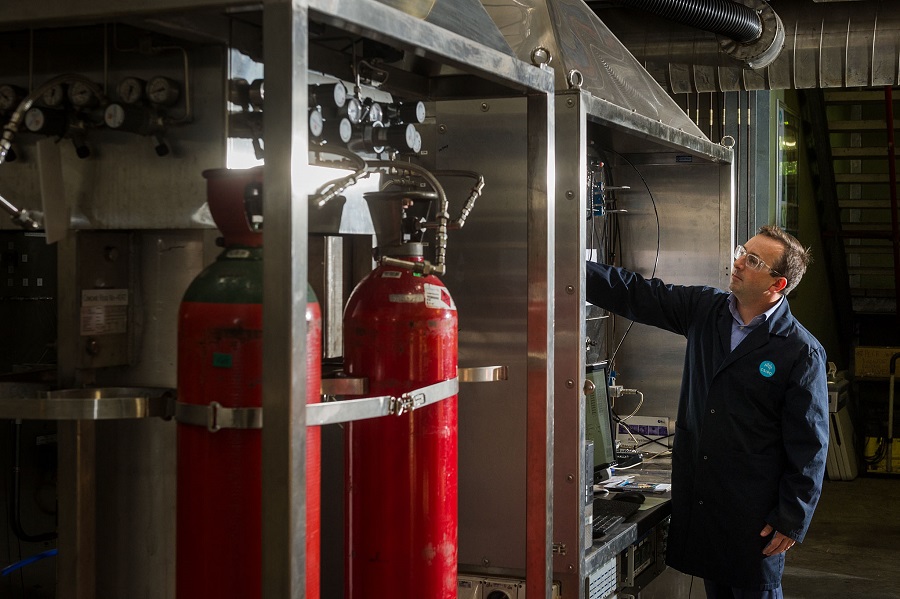
Photo of CSIRO researcher in hydrogen lab.
Dr Michael Dolan in our hydrogen lab.
It’s colourless, odourless, the most abundant element in the universe, and may one day take you from 0-100 on the highway. It seems as though hydrogen is a pretty logical choice for clean fuel of the future. The kicker is that there’s very little pure hydrogen to be found anywhere on Earth, meaning we need to somehow produce it.
There are a couple of different ways to produce pure hydrogen – it can be extracted from natural gas, though carbon dioxide is a by-product. There’s also a renewable option through the electrolysis of water, which produces hydrogen and oxygen. Forcing this reaction requires a fair amount of energy which could potentially come from a clean source, like solar.
Then there’s the matter of transporting that pure hydrogen to the places it’s needed, and if we’re planning a hydrogen-powered vehicle revolution, that means every service station! Because of its low density, hydrogen can be difficult to transport and must be pressurised, and then carried by pipeline, tanker or some other secure method. While hydrogen is already being used around the world, the existing transport infrastructure is not enough to support widespread consumer use. As a standalone hydrogen delivery system, this isn’t shaping up to be cost or energy efficient.
But rest assured there are other options … ammonia for example. Ammonia is a compound of nitrogen and hydrogen that is already transported far and wide for use in industry (as fertiliser, cleaner, etc). What if we could piggyback this existing infrastructure and transport the hydrogen within the ammonia, and then extract the hydrogen from the ammonia at, or near, the point we need it?
We have spent many years researching the best ways to separate pure hydrogen from mixed gas streams, but in this case we’re separating high-purity hydrogen from ammonia. For this very purpose, we’ve developed a thin metal membrane that allows hydrogen to pass, while blocking all other gases.

An animation shows ammonia molecules passing through a membrane to become hydrogen.
Decomposed ammonia passes through our membrane, becoming pure hydrogen.
Our membrane means that hydrogen can be transported in the form of ammonia (which is already being traded globally), and then reconverted back to hydrogen at the point of use.
While Australia is a relatively small hydrogen market, the fuel can be distributed to emerging markets in Japan, South Korea and Europe using existing infrastructure. Thinking big, we could transport Australian-made ammonia around the world so that international fuel cell vehicles could run on our hydrogen. And if we’re creating the hydrogen renewably with solar power, we are essentially exporting Australian sunshine! How’s that for home-grown ingenuity?
Our Chief Executive Dr Larry Marshall is excited by the prospect of a growing global market for clean hydrogen, and the potential for a national renewable hydrogen export industry.
“This is a watershed moment for energy, and we look forward to applying CSIRO innovation to enable this exciting renewably-sourced fuel and energy storage medium a smoother path to market,” said Dr Marshall.
Our membrane has been welcomed by industry and is supported by BOC Gas, Hyundai, Toyota and Renewable Hydrogen Pty Ltd. The project also recently received $1.7 million from the Science and Industry Endowment Fund (SIEF), which will be matched by us.
In addition to our new membrane, we’re looking forward to applying our expertise to all stages of the hydrogen technology chain (including solar photovoltaics, solar thermal, grid management, water electrolysis, ammonia synthesis, direct ammonia utilisation via combustion and/or fuel cells, as well as hydrogen production).
13th May 2017 at 10:00 pm
I have been trying to find out about the ammonia synthesis for this ‘renewable’ hydrogen. The most prevalent method for synthesising ammonia is from liquid natural gas but there is no mention how you are producing the ammonia for this technology. Can you elaborate please?
13th May 2017 at 10:25 pm
Sorry, I meant LPG, not LNG.
17th May 2017 at 3:38 pm
Ammonia is synthesized using the Haber Bosch process. This involves first making H2 (from natural gas) and N2 (from air separation). If you make H2 renewably (for example, using electricity from PV or wind to drive an electrolyser which generates H2 from water), this renewable H2 can substitute NG-derived H2 in the Haber Bosch process. This same renewable energy source can be used to drive the air separation process. Combine the renewable H2 and N2 in the standard Haber Bosch process and you get renewable NH3.
13th May 2017 at 12:46 pm
How efficient is this membrane? How large a surface area is required to get how much gas over what time period?
Is it efficient enough to be in a device like a carburettor, transforming ammonia into hydrogen for engine use – with this device giving off nitrogen as exhaust, and the engine giving off steam?
Or do you, for example, require a truck-sized transporter, just to carry the device?
17th May 2017 at 3:45 pm
We think the technology will be best suited to stationary applications like refuelling stations. Our membranes can deliver more 100 kg H2 per m2 of membrane per day, but it also depends on the recovery rate and gas mixture being separated.
2nd January 2018 at 1:06 pm
1. Could this be scaled down to supply a single 1kwH fuel cell?
As best as I can tell, the largest installed base of commercially supported fuel cells is the Ene Farm venture in Japan. There are more than 200000 residential installations. These run on re-formed methane but at least one the vendors (Panasonic) is looking at supply fuel cells running directly on hydrogen.
2. Stuart Licht and team from George Washington university has patented a novel ammonia production process that purportedly is both more energy efficient than the Haber – Bosch process and does not require natural gas feedstock (only needs air and water). I can’t find any commercial references yet , but interesting the large Norwegian ammonia producer, Yara, operating in the Pilbara is conducting some kind of solar energised pilot in the pilot starting this year (2018). It is interesting that no mention is made of the process they will use. It may just be a solar powered H2 from water..
13th May 2017 at 7:25 am
This doesn’t mention how you decompose the ammonia? I recall the ANU’s solar dish would decompose it with the high temperatures that the dish.
Does the membrane do the decomposing as well? With no additional inputs? That would make it extraordinary. Details please!
17th May 2017 at 3:49 pm
It wasn’t mentioned in the article, but our project team in Energy and Manufacturing is also working to develop an ammonia decomposition catalyst which operates at the same temperature as the membrane, at around ~400°C. The membrane itself has a catalytic surface, but doesn’t have enough surface area to allow the NH3 decomposition reaction to keep up with the H2 separation rate. We have to add a high-surface area catalyst for the process to work efficiently.
2nd January 2018 at 2:55 pm
Ideally your catalyst would consume all of the NH4 and that seems to be the direction you are going, but until that is ready, the the output stream would be predominately N2 with some unconverted NH3. Would it not be possible to moderately re-pressurize this output stream and liquify the residual NH4 out and re-input it?
12th May 2017 at 10:07 pm
I would like to see following conversion efficiencies:
(1) solar/wind to hydrogen
(2) hydrogen to ammonia
(3) ammonia to hydrogen
(4) hydrogen to wheel
With each conversion you lose a part of the primary energy (solar/wind)
Wind/solar for pumped hydro storage and then used for electric rail (low friction loss) will be unbeatable. Use of individual cars is unsustainable. Our biggest problem will be fuel for trucks to bring food to the cities. Next oil crisis coming 2020 according to the IEA
17th May 2017 at 6:15 pm
Fuel for trucks is not difficult, just use the ammonia directly!
Has been done as far back as 1943. You can displace about 95% of the fuel with ammonia with almost no changes to a diesel engine, and biodiesel is pretty easy.
I’m certain 100% NH3 engine operation in a ‘diesel’ is possible too. (assuming a specialised ignition system).
If you needed energy for the decomposition, you could get it that way too – use the waste from the cell and dispose of the H2/N2 contaminated NH3 at the same time.
Ammonia also gets used to eliminate NOx from the exhaust, so that’s easy too.
As far as the efficiency cost for H2 vehicles via NH3: From what I’ve heard, at most pessimistic, the total reduction in efficiency is currently no worse than about 2:1 compared to what you’d get going from PV straight to an EV’s wheels.
That number is the first-draft, back-of-envelope, how-bad-can-it-be calculation, and includes 1->2->3->4, as compared to PV to grid to EV wheels efficiency.
Of those I think (1) was by far the biggest energy hog, which answers the question of why not just electrolyze at the H2 pump. (2) I think had room for improvement, but again, it could go near the energy source.
(4) is already surprisingly high: H2 cars already demonstrate up to 1000km range on a tank.
That just leaves (3), which was what this breakthrough was about.
I don’t have the actual figures though, but again: Total lifecycle: Half the efficiency compared to PV -> EV.
Good enough.
Gaining the ability to endlessly store, transport and export solar energy is somewhat of a ‘killer app’ for PV farms.
The ‘low’ efficiency does mean it doesn’t really tread on the EV industry either.
If anything, it means greater demand for shorter-ranged (and thus more affordable) ‘daily driver’ cars. EV’s will have twice the mileage-per-dollar in comparison, and a lot of EV conversion costs is in the battery. If you don’t mind giving up range, you can convert your own car today for about AUD $10k.
That means more cars per battery, and more displaced cars per battery too. H2 cars at the same time have awesome range, so if you wanted to not spend time refueling, (for commercial use), then they’d be a better pick than EV’s.
Don’t mind bulky fuel tanks and a slow-revving engine with a complicated NOx absorption system on the exhaust? Ammonia.
So, high efficiency, intermittent use -> EV.
Small vehicle with longest range (and aerospace too) -> H2, or EV with ‘swap-able’ batteries.
Heavy Vehicles looking for economy, also grid backup where the batteries haven’t enough capacity -> Ammonia and/or MRC
Existing vehicles, easy/cheap conversion, 95% emissions reduction with good range -> Dual fuel with aftermarket Ammonia system. Just needs ammonia at the pumps.
Existing vehicles, expensive conversion, 100% emissions reduction, half-cost fuel but poor range -> do a DIY electric conversion! Available now: Many have!
17th May 2017 at 6:21 pm
Oh, if you want those detailed numbers for (1) through (4), you should ask Louis Wibberley ( Louis.Wibberley@csiro.au ). He’s currently working on a bunch of proposals related to these ideas — you’ll likely hear about it soon.
But the take home was: Efficiency is an issue, but not a killer.
And it gives Australia a serious contender for energy export, with a lot of flexibility and room to improve too.
12th May 2017 at 5:37 pm
The question that nobody seems to be asking is how do you decompse the ammonia in the first place before you even separate the gases? AFAIK it is energy intensive – so I am not sure what the advantage is with this. I mean why not transport it as water for example?
17th May 2017 at 3:54 pm
The problem we’re addressing is that the best renewable energy resources (for example, a large, flat, unpopulated area like the Pilbara) are a long way from the renewable energy markets (countries like Japan and Korea which have poor geography for renewable energy generation). Converting the renewable electricity to a chemical fuel is the cheapest and most efficient way to transport this energy over long distances and long time scales. If you transport it as water then you still need to bring the energy to the point of use (where it is less abundant).