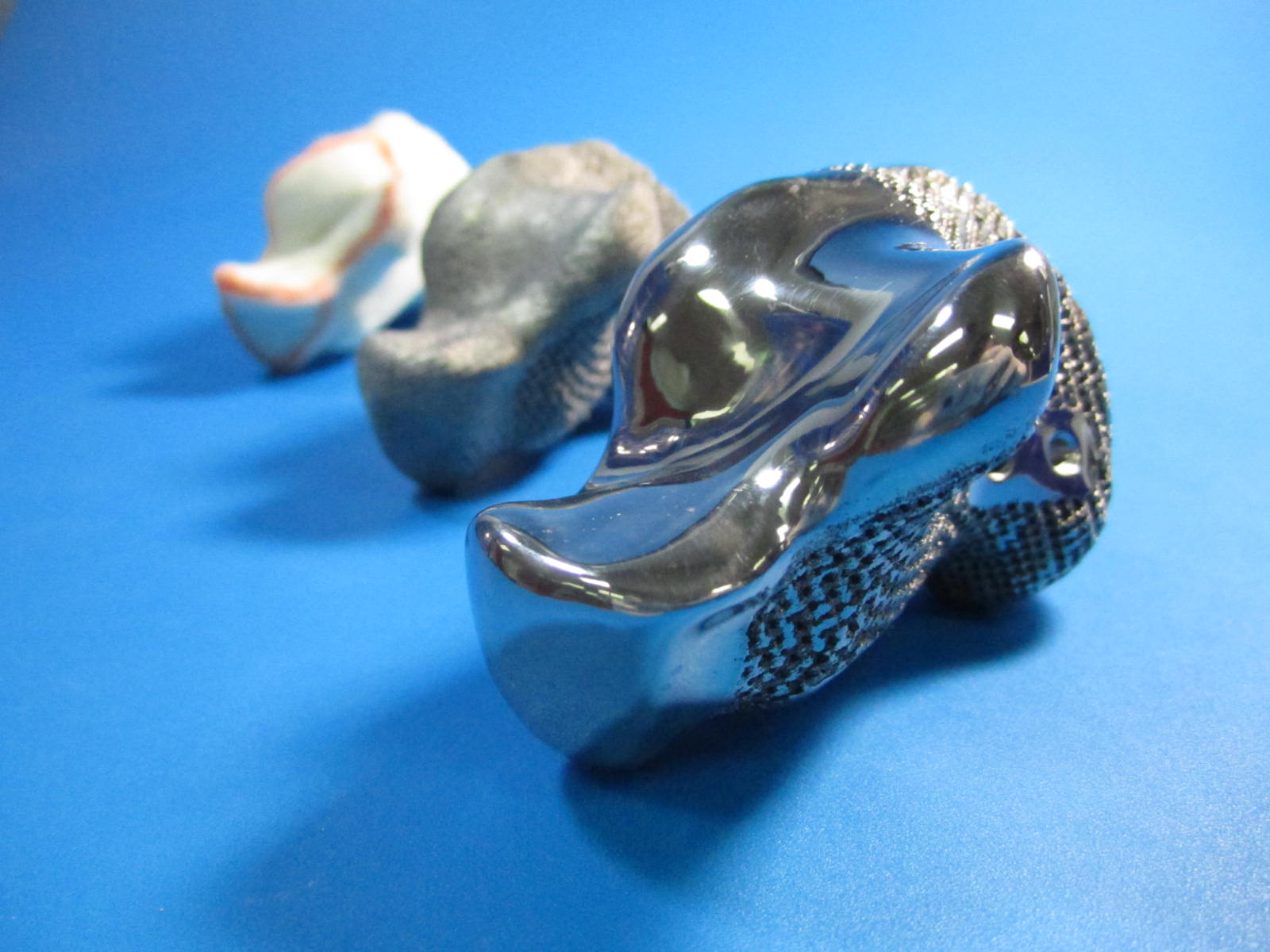
Image of a 3D printed titanium heel implant, with two other non-metallic versions
The 3D-printed titanium heel implant
This story is part of our spotlight series on #CSIROhealth. From apps to 3D printing, global epidemics to preventative wellbeing, we’re working in many ways, across many industries, to keep you healthy. More on our website.
Surgery has come a long way since the days when it consisted of either cutting things out or cutting them off. But there are still conditions where amputation is the only alternative.
One of them, until recently, was bone cancer.
Len Chandler was facing the prospect of having his leg off below the knee when he was diagnosed with cancer of the calcaneus (heel bone). Until his surgeon, Professor Peter Choong from Melbourne’s St Vincent’s Hospital, had an idea.
He knew about our work in titanium 3D, after reading about our work on producing an orthotic horseshoe in 2013. He got in touch with John Barnes, our titanium and 3D printing expert, asking whether his vision – a metallic implant which would support a human body’s weight – could become a reality.
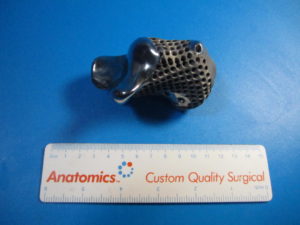
Image of 3D printed heel implant showing rough surface
3D printed heel implant. Note the rough surface for flesh to adhere to
At the time, we were working with the Victorian-based biotech company Anatomics on metallic implant technology. John brought Anatomics into the discussion, to draw on their experience as a certified custom medical device manufacturer.
Our Manufacturing Flagship worked with Melbourne’s St Vincent’s Hospital and Victorian biotech company Anatomics on a world-first surgery, developing a heel bone implant printed in titanium on our state-of-the-art Arcam 3D printer.
Working from Anatomics’ schematics for the heel bone, teams at Anatomics and CSIRO developed the design requirements with Choong’s surgical team. These included smooth surfaces where the bone contacts other bone, holes for suture locations, and rough surfaces that would allow tissue to adhere to the implant. In the days before the surgery Anatomics and CSIRO produced three implant prototypes.
The entire process, from first phone call to surgery, took two weeks. Three months after the surgery, Mr Chandler has had his most recent check-up. He’s recovering well, and is able to place some weight on his implant.
As CSIRO’s Robert Wilson, part of the heel printing team, points out, ‘The customisation of 3D printing is good in emergency situations such as these’.
It’s also a local manufacturing process: Australian companies producing implants for our own doctors and patients. That means we don’t have to rely on imported parts, and the design can be truly personalised to the patient.
We’re working with a number of major companies and SMEs across Australia to build capacity in biotech and manufacturing.
The plan, says John Barnes, is that, ‘At some point in the future we expect that local for-profit businesses will have the capacity to work on projects like this, and until that momentum is built up in local industry, CSIRO is here to help local industries gain that momentum’.
Read about our other 3D printing projects on our website.
5th March 2020 at 7:28 am
How good is CSIRO?
11th November 2014 at 11:00 pm
Nice Information. Thanks for sharing..
6th November 2014 at 11:13 am
This is one of those giant leaps for mankind that will go largely unnoticed by our mainstream Media that abhors good news but prefers instead to devote the majority of their News broadcasts to the number of daily dead in Arabic countries. Perhaps Catalyst will pick it up. Congratulations from a grateful member of the public to the very smart people who devote their lives to making life better.
21st October 2014 at 3:07 pm
Reblogged this on 3d Printing the Future and commented:
A great use of 3D printing for medical use!